Photo credits – Shahi Exports
Around mid-March 2020, the Federation of Indian Exports Organisations reported that the manufacturing sector, which contributes to 15% of India’s GDP, would be the worst hit due to COVID, particularly in the first quarter of the current financial year. With an increase in the number of active COVID cases in India exceeding 89,000, the manufacturing sector faces unprecedented challenges owing to financial and mobility shocks due to a nationwide lockdown. ILO stated that due to COVID almost 1.6 billion workers globally face the probability of losing their livelihood. The Indian apparel sector, which is the world’s 4th largest producer of textiles and garments and employs 45 million people, recorded a 16.7% fall in output in March 2020 over last year as per the Index of Industrial Production, creating a massive $2 billion hole in India’s apparel industry. Even with factories gradually opening up, there are constraints to social distancing such as high population density in factories, labour-intensive work, and negligible automation. There are also several anxieties from re-starting work about commuting, working, and interacting, among workers and managers, that need to be solved.
Recently, we collaborated with Good Business Lab (GBL) on an initiative that seeks to address pressing challenges faced by the manufacturing sector in the current context. In this post, we share some insights and suggestions from a design-thinking hackathon organised by GBL and its industry partner Shahi Exports. The two-day virtual hackathon, facilitated by external partners (including LEAD), focused on developing a set of practical guidelines to design an anxiety-free workplace experience for workers in the manufacturing sector.
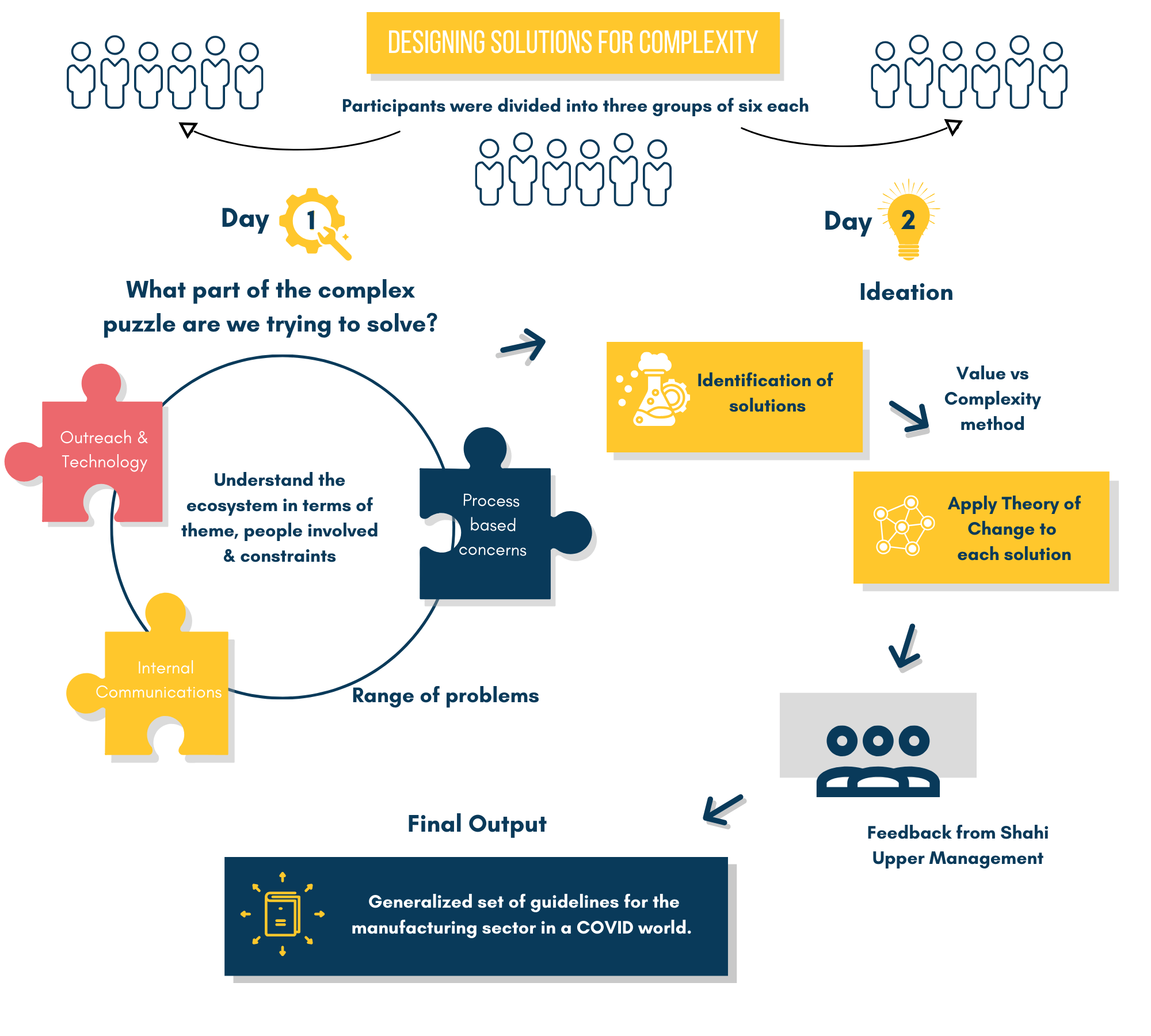
The two-day design-thinking workshop
Our suggestions from the hackathon
Consensus on the factory’s priority to be focused on “making workers feel valued” resonated across solutions. While basic measures like temperature screening and disseminating information on COVID are measures all factories must adopt, the hackathon aimed at answering the question: How can factories do this with compassion?
On re-opening, have a “day 0” with no workload
On Day 0, share welcome kits with workers, keeping in mind all aspects of worker’s health. These can include masks for workers and their families. Considerations should be made to add other essential items such as sanitary napkins and iron supplements in the kits made for a female workforce, as access to menstrual hygiene products and nutritional supplements can become restricted for the most vulnerable segments.
Go the extra mile and mobilize factory managers to write handwritten messages, to express warmth and gratitude to the workers. Maybe even organize a DIY activity where workers customize their mask, forming an emotional attachment with the mask which can encourage continued usage!
Humanize self-declaration forms
Get workers to self-declare any travel history and symptoms. Call them in advance so this does not come as a shock on Day 0. Make all employees at a factory, regardless of stature, sign this form. This is necessary for the safety of the entire workforce and to also ensure workers do not feel singled out and thereby judged, which can otherwise result in underreporting of symptoms. The tone should not be threatening. Reassure and support those who choose to stay home due to health problems with job security, wherever possible.
Let the communication around social distancing norms be considerate
The general tone of any communication should be welcoming and understanding, to elicit cooperation and solidarity.
On the factory floor, keep doors open, where possible. If you run a garment factory, use cloth scraps ready for daily activities like opening bathroom doors or touching other surfaces.
Increase space between workstations. Reimagine the organization of the assembly line if your factory runs on one. Explore alternative arrangements to reduce the number of workers in one line with one tailor taking up multiple operations.
Stagger work days – imagine shorter work weeks in manufacturing! Consider operating every alternate day or fewer number of days in a week (workers can work an extra one or two hours each day) to minimize movement and congregation of people.
To balance all the COVID-19 messaging, do simple things like putting up posters with baby pictures or grounding exercises to create a welcoming atmosphere. Also, set up counselling help desks constituted of medical and HR teams.
Introduce worker champions and celebrate these ambassadors of change
Select influential peers, who are trained to do basic screening and impart the correct health and hygiene information. They can be a crucial channel of information dissemination at every stage. Give them non-monetary rewards such as badges, certificates, and display their pictures on notice boards. Success, for example, can be judged on the number of workers in their group/line wearing masks and following hygiene instructions.
Re-think matrices of value across businesses
Be a pioneer in leading a paradigm shift to focus on “worker satisfaction” over and above “worker productivity” in public facing reports and communication along with operations as a whole. In statements to the government, and other reports begin with updates on worker wellbeing and focus on social profits along with economic profits.
Lastly, turn spare spaces into isolation wards
Turn any spare spaces into isolation wards in case any worker tests positive. This quarantine facility will help in ensuring workers that support is being provided from end to end! Companies should have additional features such as in-house testing and factory ambulance to take workers to hospitals.
Applying some learnings
The hackathon guidelines emerged in collaboration with Shahi Exports, an apparel manufacturer in India. At every stage we sought the advice of various people at Shahi – from their organizational development team members to senior level executives – on the viability, desirability, and feasibility of our suggestions.
This was the first time the factory framed policies based on the advice of an external body to such a great extent, and in the words of Mr Srinivasa Rao Venkatesh, Chief Compliance Officer at Shahi, “The entirety of Shahi’s Standard Operating Procedures came from the GBL hackathon document, conversations with the GBL team, and government best practices.” All of their 50+ factories in Karnataka and the National Capital Region of Delhi are now functioning.
GBL recommendations which were adopted by Shahi, include – forming factory level task force teams that include workers, the general welcoming tone of communication, different work and lunch shifts, flexibility in work hours where possible, counseling desks, ambulances on call, talking openly about anxiety, Day 0, and masks for workers and the wider community. They have further instructed all factory teams to focus on creating awareness, maintaining consistent communication through various channels and key people, and stated clearly in their guidelines to ‘continuously assure workers about paid leave, health care facilities from the Unit Medical Team and non-retaliation for taking sick leave.’ In fact, the idea of self declaration forms first came from Shahi, and we only fleshed out the modus operandi for it. Keeping doors open wherever possible and use of cloth scraps to touch surfaces found their way in the guidelines too.
As for those not taken up, there is hope! According to Chitra Ramdas, General Manager, Organizational Development, Shahi, “Some guidelines have not been discarded but postponed. There is a high cost of implementing everything at once. Some measures which are costly include printed posters for all factories, handbooks for all workers, and intensive training of peer educators. In fact, my team has adopted creative ways such as handwriting posters, using images from newspaper cut outs in the face of lockdown. Above all, there is a cultural change at an organizational level required that takes time.”
Closing thoughts
We all have to learn to deal with ambiguity. We are adapting to new information everyday. What we do know is that businesses that act with empathy today are securing their future. We also realise that worker wellbeing needs to be at the heart of business strategy. These guidelines can serve as a starting point for integrating worker well-being into business culture and practices and enable firms to respond to the challenges of running manufacturing operations in a COVID world.
About the Authors
Kanika Joshi is a Research Manager at LEAD at Krea University. A development practitioner with a multi-sectoral understanding of working with nonprofits across the global south, she is deeply passionate about youth empowerment, women in MSMEs, entrepreneurship and anything SDGs. She loves to leverage qualitative research for understanding grassroot realities.
Lavanya Garg is the Chief of Staff and Senior Strategy & Development Manager at Good Business Lab. She holds an undergraduate degree in Economics from Lady Shri Ram College, and a Masters in International Development Economics from Yale University.